SPENN
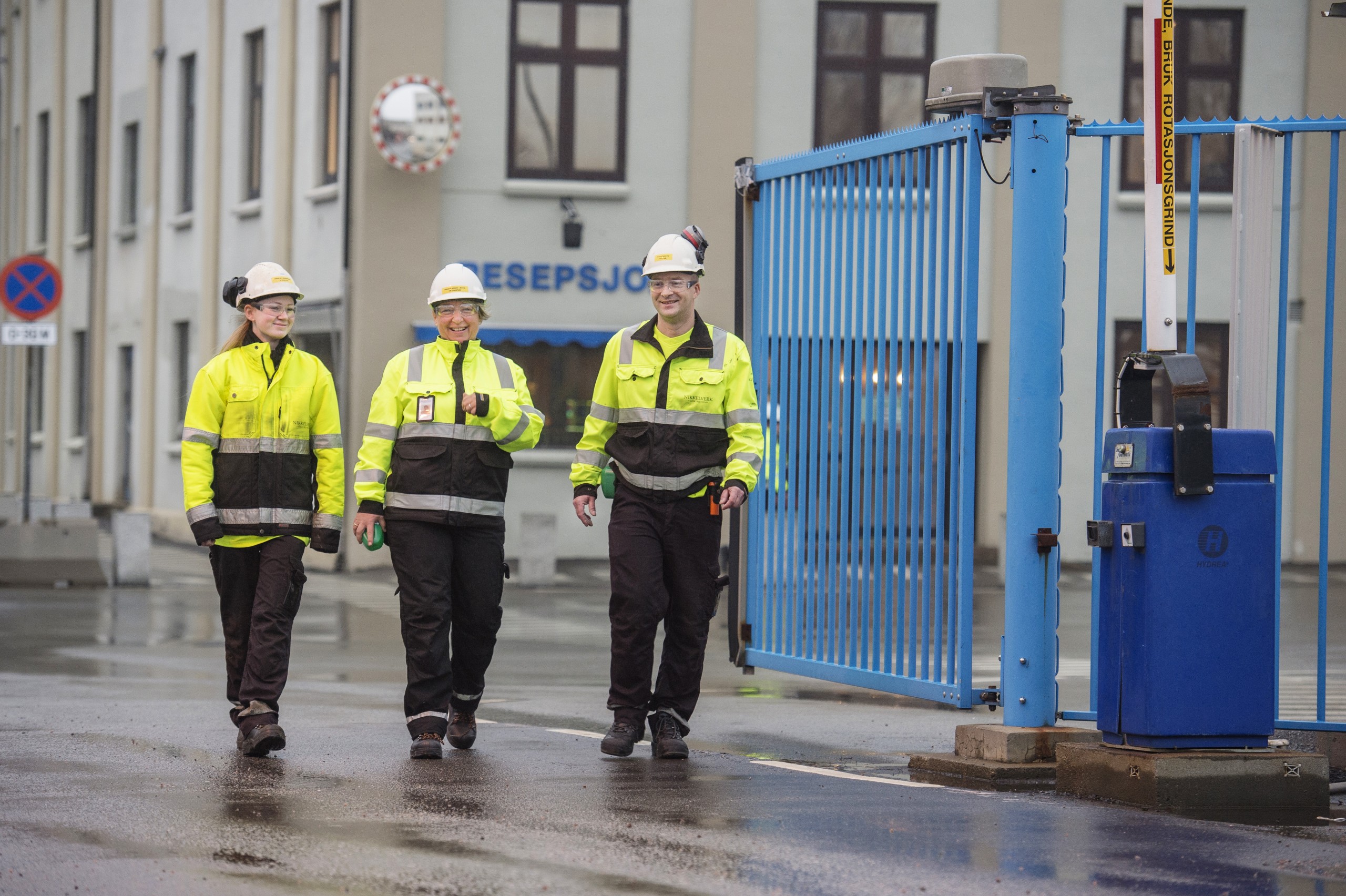
Slik ble nikkelverket ni ganger mer effektiv
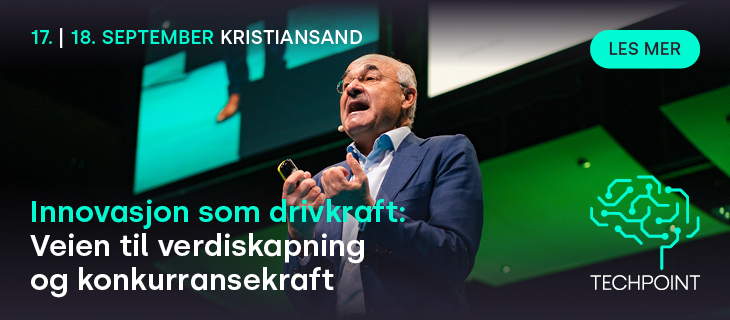
På slutten av 1970-tallet hadde 1750 mennesker sitt arbeid ved fabrikken som da het Falconbridge. I dag er antallet ansatte redusert til rundt 550. I den samme perioden er produksjonen av metaller tredoblet.
– Vi har vært helt avhengig av å bli flinkere og mer effektive. På 80-tallet følte vi på trusselen om å bli nedlagt til fordel for produksjon i Falconbridges hjemland, Canada. Siden har den sterke globale konkurransen presset oss til å bli stadig bedre, sier Ramsdal.
105 års historie.
Siden 1910 har det vært produsert metaller, først og fremst nikkel, på anlegget like utenfor Kristiansand sentrum. I starten var det to gode grunner til å etablere anlegget; tilgang til råstoff fra gruver i Evje og billig kraft fra landsdelens nybygde kraftverk.
Gunstige kraftpriser er fortsatt viktig for Nikkelverket, mens gruvene på Evje for lengst er nedlagt. I dag importeres nikkelmatte i hovedsak fra Canada – det kommer et skip til fabrikkens havn hver 14. dag, og sekundært fra en kilde i Botswana. Nikkelmatte er et halvfabrikat som inneholder 40–50 prosent nikkel, 20–35 prosent kobber og noe kobolt, jern og edelmetaller. På Nikkelverket utlutes metallene i nikkelmatten med klorgass, og nikkel og andre metaller fremstilles til slutt ved elektrolyse.
I Kristiansand produseres fem prosent av all verdens nikkel.
– Blant metallene er nikkel svært viktig. Nikkel brukes først og fremst til å lage stål og er en helt avgjørende komponent i rustfritt stål, som brukes i blant annet kirurgisk utstyr, batterier, fly og romfart. Nikkel produsert i Kristiansand finnes overalt i dagliglivet og altså til og med i verdensrommet, sier Ramsdal med et smil.
Kobberrevolusjon.
Ikke alt handler om nikkel. Siden 2007 har Nikkelverket brukt 70 millioner kroner på å utvikle en helt ny produksjonsprosess for kobber. Resultatene i et pilotanlegg, som har vært operativt siden 2012, er oppsiktsvekkende gode!
– Den nye prosessen reduserer energiforbruket med 35 prosent, og behovet for arbeidskraft med 75 prosent. Roboter tar over det meste av arbeidet. Dermed kan vi snart bruke 30 av de 40 ansatte i kobberavdelingen til andre oppgaver, sier Ramsdal.
Basert på den nye produksjonsprosessen planlegger Nikkelverket å investere en milliard kroner i et nytt fullskalaanlegg for kobber. Enova bidrar med 380 millioner kroner i støtte, mot at anlegget blir et sted hvor andre kobberprodusenter kan komme for å lære.
– Det kan høres rart ut å investere så mye, og så la alle konkurrentene komme for å lære hvordan de kopierer produksjonsprosessen, men innen kobber er det en sterk delingskultur. De ulike verkene har alltid vært åpne om nyvinninger. Mens vi hegner om produksjonsmetodene våre for nikkel, deler vi gjerne hemmelighetene rundt kobber, sier Ramsdal.
Går alt etter planen, starter byggingen av demonstrasjonsanlegget i 2017. Byggeperioden vil være på rundt tre år.
[caption id="attachment_5185" align="alignright" width="400"]
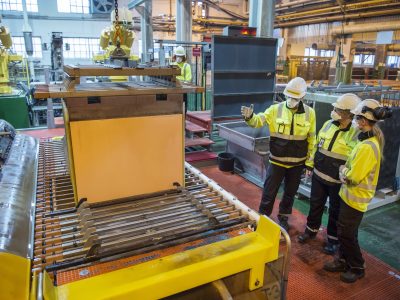
Satser på kompetanse.
At en liten kobberrevolusjon nå springer ut fra Kristiansand, kommer som et resultat av vedvarende satsing på kompetanse på Nikkelverket. I tillegg til et sterkt fagmiljø innen teknologiutvikling, har bedriften gjennom mange år vært preget av en kunnskaps- og forbedringskultur.
– Våre ansatte skal ikke bare gjøre jobben, de skal også forbedre jobben og dele forbedringene med andre. Vi er ingen tradisjonell industribedrift, men en kunnskapsbedrift, sier HR-direktør Agnete Rieber-Mohn.
I 2015 bidro ansatte ved Nikkelverket til 600 registrerte forbedringer.
– FoU-miljøet kan ikke drive utviklingen alene. Alle må bidra med ideer som sikrer vår felles framtid. Å være delaktig i denne prosessen, gjør også jobben mer meningsfull, sier Rieber-Mohn.
36 lærlinger.
I satsingen på kompetanse ligger også en stor satsing på lærlinger. Nikkelverket er en av de største lærlingbedriftene på Sørlandet og har for tiden 36 lærlinger fordelt på 11 fagområder. Nylig mottok bedriften NHOs hederspris 2015 for sin langsiktige satsning på lærlinger og etter- og videreutdanning av ansatte.
– Lærlingordningen er en veldig viktig rekrutteringsarena for oss. Etter å ha testet ut en rekke unge talenter over en periode, får de beste – rundt halvparten – tilbud om jobb. Inntak av lærlinger er del av samfunnsansvaret vårt, men først og fremst er det en glimrende måte å sikre dyktige medarbeidere, sier Rieber-Mohn.
Flere ansatte har startet karrieren som lærlinger og senere tatt videreutdanning som ingeniører eller på teknisk fagskole. Slik skaper Nikkelverket utviklingsmuligheter som bidrar intern mobilitet.
– Vi satser mye på internopplæring og oppfordrer ansatte til å øke kompetansen. Flere har nå to fagbrev. Lønnsystemet er også kompetansedrevet, sier Rieber-Mohn.